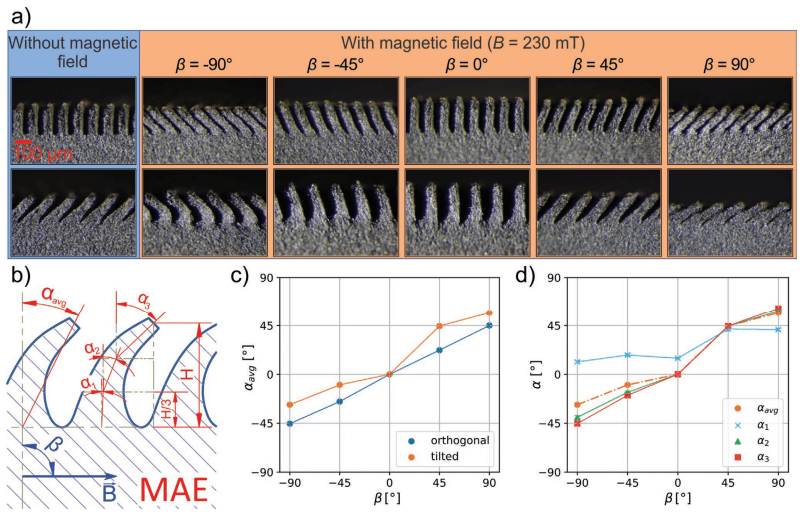
Fabricating magnetoresponsive lamellar surfaces with Memmert universal oven
Learn about a new laser-based method for creating structured magnetic actuation and emission (MAE) surfaces with a high aspect ratio with Memmert universal oven
Magnetoactive elastomers (MAEs) are hybrid materials consisting of micrometre-sized ferromagnetic particles embedded in a polymer matrix that can change their physical properties by exposure to a magnetic field. They have many potential applications such as control of surface wettability, adhesion and friction, and can be used in droplet-based microfluidics, soft robot locomotion and more. MAEs can be structured using techniques like replica moulding, magnetic particle-assisted moulding, magnetic micropillar bonding and spray coating, but there are challenges in the additive manufacturing of MAEs. There is a need for alternative microstructuring methods to expand the applicability of MAEs.
This 2021 experiment makes use of the Memmert universal oven UF30, part of the company’s drying oven series. The full study is available here.
Laser-based direct micromachining of magnetoresponsive lamellar surface structure
Schematic presentation of laser-based direct machining of MAE surface. The laser beam is guided along contours by a scanning head. Localised ablation of material along various contours results in various surface structures, such as a) parallel lamellae, b) arrows, c, d) zigzag, e) symmetrical pillars and f) asymmetrical pillars
Laser-based direct micromachining (LDM) is a process used to fabricate magnetoresponsive lamellar surface structures. The process involves impinging the surface with high-intensity laser pulses at a preselected angle of incidence using a high-speed scanning head.
Orthogonally oriented and e–h) tilted lamellar structures processed by laser direct micromachining. Structures from left to right were machined with an increasing number of laser passages along the scanning path NR = (4, 8, 16, 32). Tilted lamellae were made at a 45° angle of incidence. i) Main dimensions of structure cross-section are lamella height H, its width Ws, the width of neighboring groove Wg, and inclination angle α. j) Structure height H versus the number of repetitions NR for each lamellar structure
The LDM process allows for the creation of a wide range of microstructure geometries such as parallel lamellae, arrows, zigzag and pillars with symmetrical or asymmetrical cross-sections. The lateral dimension of the structures is typically 50 µm, while the height is more than 200 µm.
Process
The LDM process is based on the absorption of the high-intensity laser light and the subsequent fast heating of the material above evaporation temperature. The volume of the ablated material depends on the laser beam diameter and pulse energy. The heterogeneous properties of the material being machined present a challenge for consistent ablation and a laser power of 70% of the maximum power was selected in preliminary experiments to effectively ablate the material while minimising heat-affected zones and excessive fragmentation.
Experiments showed that it is possible to produce structures with a large height-to-width ratio, up to 6:1. The structures have a low modulus of elasticity, allowing the lamellae to align with the direction of an applied magnetic field. The results also showed that the depth of the grooves linearly depends on the number of repetitions of the laser beam, with a minimum lamella thickness of about 20 µm and a maximum depth of 300 ± 14 µm. The groove width remained relatively constant, regardless of the depth of the lamellae.
Deformations of magnetoresponsive lamellar microstructures. a) Deflection of lamellar structures under various orientations of magnetic field for orthogonal structures (top row) and tilted structures (bottom row). b) Schematic representation of measured slopes α of tilted lamellae under various orientations β of the magnetic field. c) The average slope of the lamellae αavg versus magnetic field direction β. d) Intermediate slopes α1, α2, and α3 of the tilted lamellae versus magnetic field direction β
The results of the experiments show that the LDM process is an effective way to produce magnetoresponsive lamellar surface structures with a wide range of geometries and high slenderness. However, further research is needed to address limitations such as the minimum lamella thickness, which is restricted by the heterogeneous composition of the material being machined.
Analysis
A new laser-based method for creating structured magnetic actuation and emission (MAE) surfaces has been developed. The process is direct and enables the formation of complex small structures. The practicality of the technology is demonstrated by creating lamellar microstructures with a high aspect ratio, which can be bent by a weak magnetic field. The sliding angle of a water droplet on the structures can be controlled by magnetic fields, making it suitable for use in applications like smart surfaces, microfluidic devices and soft robotics. The technology opens up new opportunities for further exploration and utilisation.
Experimentation and curing using a Memmert universal oven
This article describes the preparation and characterisation of magnetic anisotropy elastomer (MAE) samples. The samples were synthesised using a specific blend of ingredients, including soft-magnetic carbonyl iron powder (CIP) and silicone-based polymers.
Variation of wettability and adhesion properties of magnetoresponsive lamellar surfaces
The mixture was thoroughly blended and poured onto a polyvinyl chloride (PVC) foil and then cured in a Memmert UF30 universal oven. The surface of the samples was then laser processed using a nanosecond pulsed Nd:YAG laser. The structure of the MAE samples was characterised using a zoom stereo microscope and customised experimental setup that measured sliding angles. All statistical analysis was performed using Python. The Memmert UF30 universal oven played a crucial role in curing the MAE samples and ensuring the high quality of the final product.
About the Memmert universal oven
The Memmert universal oven, part of the company’s drying oven series, is a versatile lab oven with precise and easy-to-use temperature control. It is available in 9 model sizes with a volume range of 32 to 1060 litres and two model variants: SingleDISPLAY and TwinDISPLAY. The oven features a temperature scope of up to +300°C and users can choose between natural convection or forced air circulation. The oven is simple to operate with an intuitive menu and features programmable temperature and air exchange ramps as well as a pre-heated fresh air system that prevents temperature fluctuations.
Memmert universal oven UF30
The oven is made from high-quality, corrosion-resistant stainless steel and offers a range of options for programming and documentation using interfaces, integrated data logger and AtmoCONTROL software. It also comes with a 3-year worldwide guarantee. Additionally, the Um model can be used as a medical device for heating fango, silicate and APS packs for physical therapy. Contact us to learn more about Memmert’s heating and drying ovens and to discover the perfect solution for your individual needs.